Pre-Heater Application Heat Exchanger Review
Heat Exchanger Knowledge | Heat Exchanger Companies Suppliers
In large steam systems, or in any process requiring high temperatures, the input fluid is usually preheated in stages, instead of trying to heat it in one step from ambient to the final temperature. Preheating in stages increases efficiency and minimizes thermal shock stress to components, as compared to injecting ambient temperature liquid into a boiler or other device that operates at high temperatures.
In the case of a steam system, a portion of the process steam is tapped off and used as a heat source to reheat the feedwater in preheater stages. Figure 8 is an example of the construction and internals of a U-tube feedwater heat exchanger found in a large power generation facility in a preheater stage. As the steam enters the heat exchanger and flows over and around the tubes, it transfers its thermal energy and is condensed. Note that the steam enters from the top into the shell side of the heat exchanger, where it not only transfers sensible heat (temperature change) but also gives up its latent heat of vaporization (condenses steam into water). The condensed steam then exits as a liquid at the bottom of the heat exchanger. The feedwater enters the heat exchanger on the bottom right end and flows into the tubes. Note that most of these tubes will be below the fluid level on the shell side.
This means the feedwater is exposed to the condensed steam first and then travels through the tubes and back around to the top right end of the heat exchanger. After making the 180 bend, the partially heated feedwater is then subjected to the hotter steam entering the shell side.
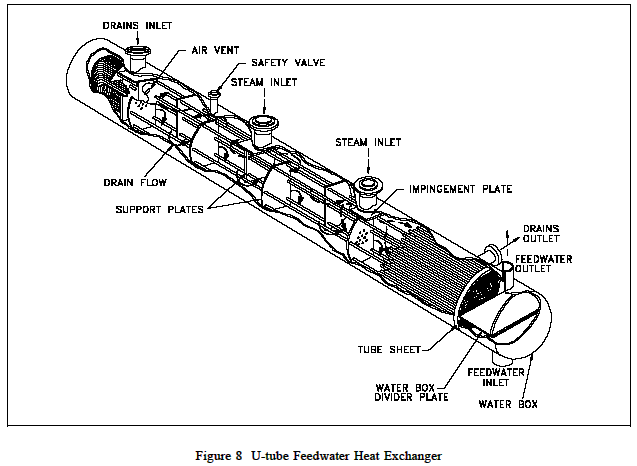
The feedwater is further heated by the hot steam and then exits the heat exchanger. In this type of heat exchanger, the shell side fluid level is very important in determining the efficiency of the heat exchanger, as the shell side fluid level determines the number of tubes exposed to the hot steam.